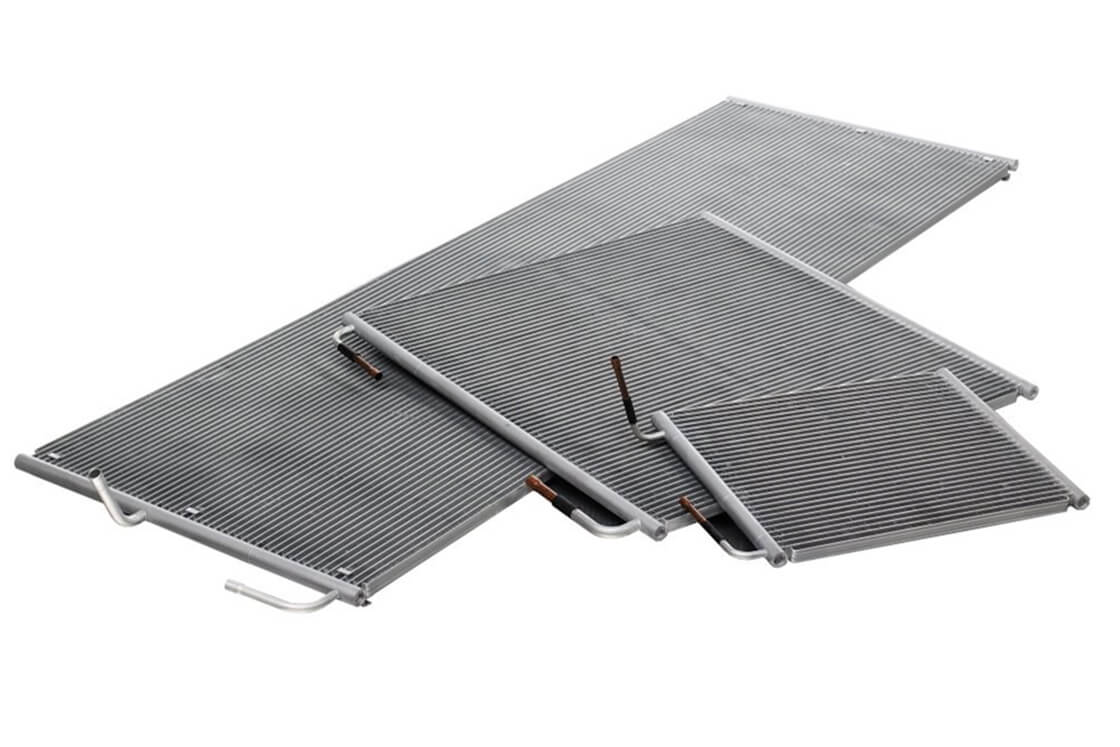
In the realm of industrial equipment, the evolution of thermal management technologies has been marked by the advent of Microchannel Heat Exchangers. These sophisticated heat exchange systems represent a pinnacle in engineering precision, delivering unprecedented efficiency in diverse industrial applications. In this article, we will embark on a deep dive into Microchannel Heat Exchanger technology, exploring its key principles, applications, and the remarkable advantages it brings to the forefront of industrial thermal management https://www.kaltra.com/microchannel-heat-exchangers.
Understanding Microchannel Heat Exchangers: Engineering Precision Unleaashed
Core Principles of Microchannel Heat Exchangers:
Microchannel Heat Exchangers operate on the fundamental principles of heat transfer through a network of microscale channels. Unlike traditional heat exchangers, which rely on larger passages for fluid flow, microchannel technology leverages numerous small channels to enhance heat exchange efficiency.
Engineering Precision in Design:
The efficiency of Microchannel Heat Exchangers lies in the precision of their design. Engineers utilize advanced computer-aided design (CAD) tools to optimize the layout of microchannels. This meticulous approach ensures optimal thermal performance, making Microchannel Heat Exchangers a cornerstone in modern industrial processes.
Materials Selection for Superior Performance:
The construction of Microchannel Heat Exchangers involves high-grade materials, often aluminum or copper alloys, chosen for their exceptional thermal conductivity. These materials contribute not only to efficient heat transfer but also to the durability and longevity of the heat exchangers.
Applications Across Industries: Harnessing Efficiency
Automotive Cooling Systems:
Microchannel Heat Exchangers play a pivotal role in automotive applications, particularly in the cooling systems of vehicles. The efficiency of heat dissipation contributes to improved engine performance and the management of increasingly complex thermal loads in electric vehicles.
Electronics Cooling:
In the electronics industry, where precise temperature control is paramount, Microchannel Heat Exchangers prevent overheating of electronic components. This application ranges from servers in data centers to sensitive electronics in industrial settings, ensuring reliability and longevity.
HVAC Systems:
Heating, ventilation, and air conditioning (HVAC) systems benefit significantly from the efficiency of Microchannel Heat Exchangers. Their compact design and superior heat transfer capabilities contribute to energy efficiency and improved overall system performance.
Renewable Energy Applications:
Microchannel Heat Exchangers are instrumental in various renewable energy systems. Their efficiency in transferring heat is crucial for harnessing and utilizing sustainable energy sources, including solar thermal and geothermal applications.
Advantages of Microchannel Heat Exchangers: Unparalleled Efficiency
Optimal Heat Transfer Efficiency:
The microscale channels within Microchannel Heat Exchangers promote turbulent flow, enhancing convective heat transfer. This results in optimal heat transfer efficiency, ensuring precise temperature control and rapid heat exchange.
Compact Design for Space Optimization:
A distinguishing feature of Microchannel Heat Exchangers is their compact design. The microscale channels allow for a higher surface area-to-volume ratio, facilitating a compact and lightweight design. This feature is particularly advantageous in industries where space optimization is crucial.
Durability and Reliability:
The use of high-grade materials and precision engineering contributes to the durability and reliability of Microchannel Heat Exchangers. These qualities are essential for industries requiring consistent and dependable thermal management solutions.
Energy Efficiency in Industrial Processes:
Microchannel Heat Exchangers significantly contribute to energy efficiency, reducing energy consumption in various industrial processes. This aligns with the growing emphasis on sustainable and eco-friendly industrial practices.
Considerations for Implementation: Ensuring Success
Application-Specific Requirements:
Understanding the specific thermal management requirements of the application is crucial when implementing Microchannel Heat Exchangers. Factors such as temperature ranges, flow rates, and space constraints should be carefully considered.
Materials Compatibility:
Ensuring compatibility with the fluids and materials involved in the industrial process is essential. This consideration contributes to the longevity and effectiveness of Microchannel Heat Exchangers in specific applications.
Customization Options:
Microchannel Heat Exchanger technology often offers customization options to meet the diverse needs of industries. This allows for tailoring the heat exchangers to specific requirements, ensuring optimal performance in various applications.
Conclusion: Unlocking the Future of Industrial Thermal Management
In conclusion, the efficiency unleashed by Microchannel Heat Exchanger technology marks a significant advancement in industrial thermal management. Its precision engineering, coupled with versatile applications and unparalleled advantages, positions Microchannel Heat Exchangers at the forefront of modern industrial processes. As industries continue to prioritize efficiency, reliability, and sustainability, the adoption of Microchannel Heat Exchangers is poised to shape the future of industrial thermal management, unlocking new possibilities and setting higher standards for efficiency in the industrial landscape.